Expanding your roof sheet production capabilities is a strategic move that can significantly enhance your business’s efficiency and profitability. When embarking on this journey, selecting the right roof sheet machine is paramount. Here’s a more detailed exploration of the key factors to consider when making this crucial decision:
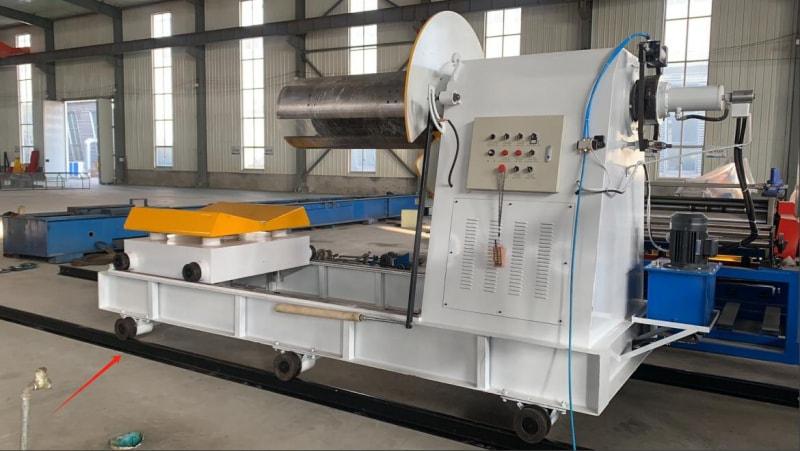
- Enhancing Automation for Greater Efficiency and Cost Savings
As your business grows, manual processes can become a bottleneck, impacting productivity and increasing labor costs. Upgrading to a fully or highly automated roof sheet machine is essential. By investing in a hydraulic decoiler and automatic stacker, you eliminate the need for manual handling of roof sheets and coils. This not only streamlines the production process but also significantly reduces the risk of injuries to workers. The hydraulic decoiler, with its rail-mounted design, offers flexibility to work seamlessly with various roll forming machines, further enhancing operational efficiency. - Durability and Precision through Advanced Machinery Components
When selecting a new roof sheet machine, opt for one equipped with a gearbox transmission system and a cast iron machine structure. The gearbox ensures smooth, rapid, and stable operation, minimizing downtime during startups and shutdowns. This durability is crucial for maintaining a continuous production flow and reducing maintenance costs in the long run. Moreover, cast iron construction adds strength and stability to the machine, ensuring precision in the forming process and extending its lifespan. Our extensive experience in designing and manufacturing such machines for diverse clients underscores their reliability and performance. - Tracking Cutting Technology for Speed and Accuracy
Incorporating tracking cutting technology into your roof sheet machine is a game-changer. This advanced feature allows the cutting mechanism to move in sync with the moving roof sheet, eliminating the need for stopping and starting. With a maximum speed of up to 50 meters per minute, it significantly boosts production rates. Furthermore, the use of servo motors ensures that the cutting process is both fast and precise, minimizing waste and enhancing the overall quality of your roof sheets. This precision is vital for meeting customer specifications and maintaining a competitive edge in the market. - Customization Options to Suit Your Unique Needs
No two roof sheet production lines are alike. Therefore, it’s essential to consider customization options when choosing a new machine. Look for a supplier that offers tailored solutions based on your specific requirements, such as sheet thickness, width, and material type. This flexibility ensures that your machine can seamlessly integrate into your existing production setup and cater to future expansion plans. - After-Sales Support and Maintenance Services
Finally, don’t overlook the importance of after-sales support and maintenance services. A reliable supplier should provide comprehensive training for your staff, ensuring they can operate and maintain the machine effectively. Additionally, prompt technical assistance and regular maintenance checks can help prevent breakdowns, optimize performance, and extend the machine’s lifespan.
In conclusion, expanding your roof sheet production requires careful consideration of the right machinery. By prioritizing automation, durability, precision, customization, and after-sales support, you can make an informed decision that will drive your business forward.